During my encounters with global business leaders, I am frequently asked the question of what is the difference between Lean Six Sigma (LSS) and Outside-In thinking and practice?
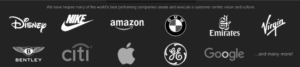
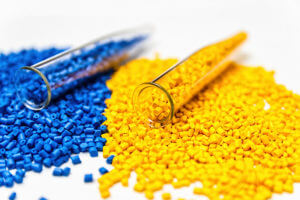
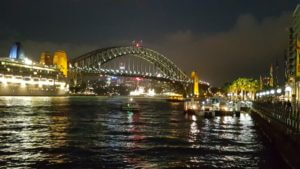
Table 1: Comparison of some differences between Lean Six Sigma and the CEMMethod™.
Element
|
Lean Six Sigma
|
Customer Experience Management/Outside-In
|
Mindset
|
Industrial Age
|
Customer Digital Age
|
Focus
|
Improve current work
|
Align to achieve SCO’s
|
Intent
|
Process will exist at the end of a review
|
Processes may be removed
|
Results
|
Focused on improving outputs
|
Focused on delivering Outcomes
|
Cost reduction
|
Triple Crown achievement (Cost/Service/Revenue)
|
|
Structure
|
Accepts the functional hierarchy
|
Proposes the appropriate structure to deliver SCO’s
|
Techniques
|
Effect based activity (value/ non-value added – waste identification – SPC etc.)
|
Causal based activity (what creates the work in the org. then let’s fix the causes)
|
Intelligent Processes
|
No mechanism exists to ensure processes are intelligent
|
Specifically designed to implement and mature intelligent processes
|
Customer
|
End to End working e.g. SIPOC
|
Centric working – the customer is at the heart of everything that happens
|
Are at the end and the beginning of processes
|
Are enlightened, Promiscuous, Rebellious, Prosumer, Multi-channel, high expectations
|
|
Enterprise objectives
|
Operational and tactical. Aims to fix process.
|
Strategic and Operational. Aims to implement a sustainable architecture.
|
Scope
|
Process based improvements
|
Enterprise-wide transformation
|
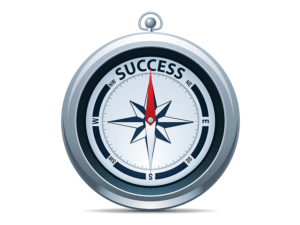
CEMMethod™: www.cemmethod.com
Certified Process Professional: www.certifiedprocessprofessional.com
Training: www.bpgroup.org/training.html